Serial Communication With Labview Tutorial Block
Below you can find the test code to check the serial communication using LabVIEW. In this code serial monitor will always display zero but in. Now in LabVIEW you have to just pick and place all the icons from library to block diagram. Now just collect the blocks one by one and place it on blockdiagram.
- Serial Communication With Labview Tutorial Blocked
- Labview Tutorial Pdf
- Labview Usb Serial Communication
Hello.
I use pl2303HXA (usb to UART converter) in my design data and sending of microphone for pc in LabVIEW 2013 x 86.
When I tried in a terminal CODEVISION, everything is OK and each microphone send to a PC, Hypertermial or Terminal CODEVISION is received correctly.
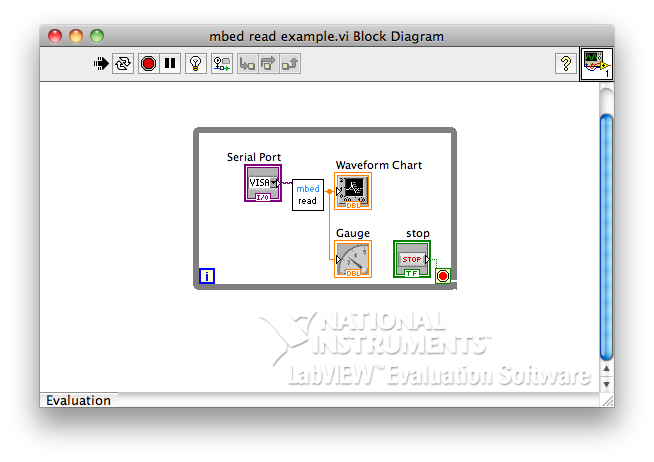
but when I run LabVIEW, it works for a few seconds and Communication all of a sudden abrupt and LabVIEW crash. You can see in picture I capture from my Telechareger below. Why LabVIEW hang?
the image is the front of my VI.
every time it blocks, I have to restart LabVIEW and test again. in the meanwhile I have to said hang occur randomly.
Thank you.
Tags: NI Software
Similar Questions
I have a question about how LabVIEW opens a serial port for communication. I communicate with a device that uses a protocol owner. It sets and clears the parity bit to indicate the nature of the response. For example, the orders are sent with the parity bit higher while responses are sent with the weak parity bit (unless the answer is at the end of the transmission, in which case the device sets the parity bit high to indicate).
My problem is the way that LabVIEW opens the serial port for communication. Using Portmon, that I captured the control indicators, that it sends to Windows to configure serial communication:
Note the values 'Shake' and 'replace '. In my view, they are originally bytes with parity errors is removed. A separate RS232 Comm Debug tool that I use with success looks like this:
Notice the difference in values. By using this tool, Windows does not packages with parity errors - that's what I want. Is there any way to change how LabVIEW opens the serial communication port to achieve?
I tried to change the parity, where the ILO is defined differently, but I think that I am running in a race condition; LabVIEW can not run the code and change the mode of fast enough parity before the next byte of data is sent by the device.
Ravens fan: the parity bit, in the proprietary protocol, that I use, is not used for parity checking. Basically, the protocol uses a 9-bit serial communication. The parity bit must be paid or compensated according to what byte do (if it is a command, if it is the end of transmission, etc.).
I found an old post on this page which seems to answer my question (my apologies for not completely research before posting.. I learn the right use/search phrases that I find more information). I download the 3.4.1 version of VISA now.
I use NEITHER myRIO for my robot and I want to use four reading of the distance sensors that communicate via the serial port. But the myRIO has only two UART ports on board so I was wondering if there is a way to program the digital pins use for serial communication. Any help appreciated.
It is possible. Here is an example that I could find.
Hello
I'm trying to control a micro-positionnement made by Ludl stage. The model is Ludl MAC2000. It seems that the RS232 comunnication is implemented because I can talk to the controller using HyperTerminal. However, when I want to do the same thing through Labview, I can't answer the controller at all. The vi is roughly the same as the visa basic read/write in the example. Looks like a very similar problem in this post:
But the trick of nature of endpoint does not help in my case: I tried to toggle the termination character setting in the property node and different combinations of 'r', 'n' as termination characters, but nothing has worked so far.
Seems to me there is some difference between the interpretations of the same order to Hyper Terminal in Labview. But I just can't understand what it could be.
Anyone with a similar experience could give me some comments/suggestions? Thank you very much!
Another difference between hyperterminal and labview is the speed of sending characters.
LabVIEW breaks out the whole string to the controller
HyperTerminal is this character by character. So much slower and slow the controller can be affected by this.
You could add a loop around the writing of visa (to make it easy convert the string into a byte array outside of the loop and convert it to a string inside and you have a shipment char by char in LabVIEW
Hello world
I have a lot of help with my project of this forum and I'm looking for more . Thank you for taking the time to help. Please bear with my as I ask a LOT of questions.
I intend to control a frequency converter using its series terminals and send orders from my PC + LabVIEW it. The commands do the basic functions like, start, stop, speed up/down etc etc. I use a converter Series USB to transfer data.
Now, I ve played with examples like SERIAL COMMUNICATION VI and others and I begin to understand the functioning of VISA.
Q1. In order for LabVIEW + VISA contact my frequency converter, do I need to install some sort of a driver for him to recognize? The frequency controller is old ages, even I don't know and I don't think I can find a driver for it any time soon? What kind of driver I'm looking for? Is it possible to customize my own driver and which would be easy?
accessory included - process.jpg
I downloaded some pictures about the problems of data format. I need to send information to the converter to format 'telegram' as shown in the image below. Each 'function' in the 'format telegram' has varied length in bytes: some have 1 others have 2, other 4..
I also downloaded an image called 'Format.jpg' which indicates what information each of these 'functions' will contain. Note:-the frequency converter uses only the last 4 bits.
Say for example:
START function will have this bit of information-
Start the Byte - ASCII ' 59 '
Address - 00
Control character -? I'm not sure what it should be I need to use the converter based on parameter values - is confused on what to choose - C, U, I or r Start, stop, etc. have their own specific parameter values such as 402, 404 RESP, so I guess I want update (U)?
Word of State control -? depends on the previous action
Sign - do not necessary
Data - 0
Comma - is not necessary
check the sum - is not necessary
Stop the Byte - ' > ' (ASCII: 62)
Phew.. How would I go about clubbing this whole format together to send a control signal? Put all this information in a table allow somehow?
Please help to me.. to achieve desperately need..
Thank you Xbox 360 emulator for pc.
Sandeep
It would be useful that you could find a driver, but it is not absolutely necessary to have a. You can write your own, use the Instrument i/o Assistant, or use VISA readings and some discreet.
The format of the commands is a bit complicated but not impossible. You just need to be careful to have the exact number of bytes.
What I don't see in the atttachments, it is possible words to control and the State and the number of parameter. I hope these are in another part of the manual.
A bytes example (without the control and settings) to update the frequency to 12.34 could be '<00U________+123403??>'.
Hello
I'm set to do a serial with Labview. The problem is that the program always crash (no popup error but only LabView don't freeze) when I read or write with VISA.
I work with a module converter (ADAM 4571) that convert Ethernet to RS-232/422/485. The module is mapped to the computer and the similar work as a COM port. I tested the connection with the Terminal windows and its work. This means that it is not a hardware problem.
I did the same communication a few weeks with the same material and did not have a problem. I don't understand why it does not work now.
I give my code as an attachment, but it is not something special except for the block that buffered (which is required for my module), but if I remove it the problem persists.
Does anyone have an idea what can be the problem?
Thank you
Jérôme
OK, I solved the problem.
The version of the driver for the converter module mapping was not exactly right, now I change it and its work.
Jérôme
I have trouble to get LabVIEW to display the bytes I send from a microcontroller with a FTDI chip.
Specifications of communication are:
baud-19200
-8-bit word length
-1 stop bit
-no parity
-no flow control
I modified the demo of the chain of read-write of the here just reading the chip. I see that a few bytes have been read in the indicator 'bytes read' but nothing appears in the buffer. Any ideas? I may have something hooked up wrong or something wrong in communication specifications
Hi I have an anemometer which I am trying to communicate with via the serial interface. I am connected via a USB converter to 485. The manufacturer of the anemometer provided two scripts of term tera to communicate with the device. When I run scripts in tera term anemometer reacts as expected. When I imitate (or so I think I'm) orders in Labview, I get no response. Please see the attached document for more information.
I'm not familiar with the language of terms of Tera, but what I found on the internet I guess that there is more information (CR & CRLF variable defined by the code2str function), which is in fact the echo back on display '00TR 00012 '.
Any ideas?
Thank you
-Scott
It is probably sending a return trolley/line. (or just one or the other).
I suggest using a program like Portmon using Teraterm to see what is actually sent and received.
Hello world. I need your help with my program. I use LabView2014 and a B2902A Agilent.
I want to measure the current value with my instrument continuously, store the values of every second and the display of the messages received through the serial port when I'm gone.
Everything works perfectly separately, but when I put everything together I have this problem: my instrument is waiting for a message from the serial port to take (and display) a measure.
You have an idea to save my problem?
Thank you!Pauline
(Please find attached a screenshot of my program)
Use the byte to serial port to check if a message is available and read only when a message is available.
Hello
I have developed a RS422 driver in LabVIEW for the basic operation is as initialize, reading, writing, closing etc. Later I used it as a library wrapped in TestStand scripts.
The question is, when I try to read the answer to one of the command, I am able to observe it in the iteration 6th step of reading, where I'm supposed to read for the first time.
Please suggest any ideas on what could be the reason.
You need to know if the response data really who arrives late, after giving a command or the VI you wrote is not able to capture the correct data.
If you have a recorder RS 422 or bus Analyzer then it will be easy to analyze the cause.
Since you are able to read step 6 on reading a few questions:
You are still able to read on the 6th read-only? If yes then probably the target USE responds slowly to this command or it sends too much unnecessary data that are read by the 5 first readings. (depends on your reading algorithm).
Playback vi must be written such that it will be in a loop (with some time out) until it gets the required data. The expiration time should be configurable.
Also before sending the order you must ensure that the buffer is empty (rinsed).
I hope this helps.
Ravi
I am communicating with a host machine that spits out data on the serial port. I'm using fairly standard settings (9600, 8, N-1) and I'm getting data.
The problem is the formatting of the data. Obviously, the data are supposed to be fixed width, but the fields are moved after each CR/LF.
Some examples of data:
0 0.925. 0,833 110.444 549.278 23.812
2
0 0,921 0,832 106.971 480.604 24.464
3
0 0.926 0.831 114.320 555.821 23,785
4
0 0.920 0.830 108.434 587.374 23.411
5
0 0.925. 0.836 106.459 554.808 23.717
6
0 0,923 0.830 112.048 507.875 24.242
7 0
0.924 0,837 103.943 605.860 23.181
8 0
0,921 0.831 108.303 582.447 23,459.
9 0
0.925. 0,827 118.501 426.680 25.118
10. 0
0,922 0,826 116.223 483.567 24.527
11. 0Any ideas what may be the cause? There the series parameters that may change the data format? I get the same results using LabVIEW and hyperterminal.
I have No control over the host (long story).
Thanks for your help.
Set the properties of your VISA to 'activate the term on readings tank' = TRUE and 'term char' = 0x0A (line feed). Configure your reading to read MORE characters that you expect and each reading will end when we see a 0x0A. (you can remove the warning from VISA if you wish.
-What happened to the cursor - this lack of cursor's post a little harder! Laura_F - is this known?
I followed a tutorial online to start learning basic communication series. The involved tutorial shorting pins 1 and 3 on port 1 Comm and write a simple program (attached). I've edited it a bit, the program to see varied results I get when trying to write and read a simple sentence via a serial port.
Could someone explain what causes the kind of result shown in 'Serial Comm example.png'? I think it has to do with timing. Why would be transmitted only the parts of the sentence?
Thank you
Sarah
sarahzig wrote:
The involved tutorial shorting pins 1 and 3 on the Comm 1 port
What should be pins 2 and 3? On a standard serial port DB-9, pin 2 is the receive and pin 3 is the transmission.
Now for your code..
1. move the Serial Port to be before the loop to set it up. Simply configure the port once.
2. close the port after the loop.
3. managing your error after closing.
4 stop your loop on an error or the stop button has been pressed. You will need a RC in there.
5. no need to Flush Buffer function. Remove it.
6. using the bytes to the Port is a dangerous thing. It introduced all kinds of race conditions that are interesting. Instead, say VISA reading to read the number of bytes that you expect to read.
6a. Moreover, don't forget to send a character to end of line at the end of your data and all the number of bytes to read something a lot more than you ever expect read. The VISA read will stop reading when he a) sees the number of bytes, it was said to read, b) sees the stop character (currently enabled and set to a line break, which is part of the end of line), or c) the time-out occurs. Whichever comes first.
7. with 6, the wait is no longer necessary.
Hello community,
I have a problem: I'm using LabVIEW to communicate with a CPU with RS232, but the program is extremely slow. In this configuration (it's a minimal example), it takes about 8 seconds to send a new string. What could be wrong? (I'm a beginner)
The program of mission is to prepare a string containing incrementing values and send over the UART.
Thanks for your help!
Greetings!
The yellow bulb is to highlight execution. It is strictly a debugging tool. Your turn that to slow down execution and be able to see how the data passes through the wires.
Disable execution of climax, and it will run at full speed.
But how do you use this VI? You have not a while loop and you have not told me if an another VI call this VI. So this VI runs only once and then stops.
(Please don't tell me you use run continuously the button which is also strictly a debugging tool.)
I recommend you watch the LabVIEW tutorials online
LabVIEW Introduction course - 3 hours
LabVIEW Introduction course - 6 hoursHello
I noticed that when LabVIEW (8.6 but before as well) application that uses VISA is installed (by building the Installer) port UDP 6000 is blocked and no other program can use it.
Does anyone know how to check that the other ports are blocked by VISA?
Thank you
Pawel
Hello
I m a newbie really in Labview and would generate an own serial Protocol.
I m using an NI USB-6363 data acquisition
My logical State should look like this:
And then I want to generate a command like this with my 0110 1101 Protocol for example.
Can someone help me to implement my idea in Labview?
THX
At least, you have chosen a DAQ with timed material DIO card.
Start looking in the viewfinder of the example (help-> examples find) for an example, called 'digital - finished Output. This example should help you get started for the release of your waveform.
Maybe you are looking for
I can't add shipping address to the Japan order a photo book. He said 'the information in the following areas is missing or incomplete: State value 'Chiba' was not found in the list of valid values.» I get a value any is not valid. Help, please
After installing 4.0, I could see is no longer my bookmarks in the sidebar, but they were accessible by clicking on the bookmarks in the Navigation toolbar. I uninstalled 4.0 and reinstalled 3.6.6 but now my beloved file system is absent from the sid
POSSO USAR O GOOGLE CHROME PESQUISAS PROVEDOR COMO O PROBLEMA COM O WINDOWS FAITH RESOLVIDO
When I tried to install turbo tax I kept getting erroe code 1601, who sends me to windows update to get the Installer 3.1 - but it fails everytime I try
I want to download the youversion bible app on my PC running Windows 7, the icon is windows8, but if I click on it nothing happens. Should I consider that youversion may not run on windows 7
Table of Contents
Here are some building blocks to interface an mbed with LabVIEW, allowing LabVIEW programs to interact with the real world. This could be used for things like:
- data acquisition in LabVIEW via sensors connected to mbed
- controlling actuators connected to mbed from LabVIEW
- LabVIEW programs with hardware-in-the-loop, where sensors and actuators are interfaced with mbed but calculations and control are in LabVIEW
We've created two ways for you to interface between LabVIEW and mbed.
- LabVIEW RPC This allows you to directly control the mbed using the RPC. For many applications it wouldn't be necessary to write any custom code for the mbed.
- Serial Communication These examples show how data can be transfered between the program running on mbed and your LabVIEW application.
LabVIEW Setup¶
To use mbed with LabVIEW, you need to have the NI-VISA drivers installed to give access to the USB serial port.
- http://www.ni.com/trylabview/ - LabVIEW trial version
- http://www.ni.com/visa/ - NI-VISA drivers for the serial port
With LabVIEW and NI-VISA installed, you should be ready to go.
We've created a set of vi's that expose a lot of the mbed interface using RPC. The vi's we've created allow you to create and control new objects or control objects that are created in the mbed code.
The LabVIEW vi's¶
Here are the vi's that allow you to interface with the RPC and some examples of their use.
- LabVIEW vi's: mbed_LVLibrary.zip - NB: For consistency the name of mbedSerial has been changed to SerialRPC
- Examples: mbed_LabVIEW_demos.zip
- LabVIEW Libraries for versions 8.5 and 8.6: LabVIEW_Previous_Version.zip
Relinking Files
When you download the files (especially the demos) they may not be in the same locations relative to the files they depend on as they were on the computer they were developed on. LabVIEW is very good at relinking files so just okay error messages or reconnect the files according to the locations in which you have saved them.
Using the LabVIEW RPC vi's¶
The LabVIEW vi's have been created to mirror the mbed api as closely as possible. They therefore take a similar object oriented approach. We create an mbed object and then using this create objects for each of the inputs and outputs.The vi's are contained in two folders:
- The 'mbed Interface' folder includes all the vi's for creating and controlling inputs and outputs on mbed.
- The 'Transport Mechanisms' folder contains the vi's for creating a connection to an mbed and then closing it.
We've provided the vi's as a zipped file which you can extract to any where on your computer. To make it a bit easier to access them we've also created a Library which might be a bit easier to develop with as you can drag vi's in from it. Just open the file mbed_LVlibrary from within LabVIEW.
Using the API¶
Information
To use these vi's your mbed needs to be running code which can receive and execute RPC commands. Information and examples of this, can be found on the Interfacing-Using-RPC page. Compile and run the program for RPC over serial to use the vi's on this page.
- First create an mbed interface by using a transport mechanism. This can be either SerialRPC or HTTPRPC.
- You can now create objects on mbed such as DigitalOut or AnalogIn. Wire up the input of a DigitalOut to the output from mbedSerial
- To create an object connect controls or constants to the pin number. Pins are passed as a string eg 'p21' or 'LED1'
- If you have an object created on mbed then you can tie to it by passings its name as a string into the existing object name.
- You can now execute the methods that are defined in the mbed api. For example you can execute a write block on a DigitalOut to set the value of the pin. Wire the write block to the object you want to act on and then add a control to set the value of the pin.
- Finally wire up the SerialRPC_delete method to the mbed wire so that the serial port is closed and is avaliable to other programs.
This is demonstrated in the LED flash example the block diagrams for which are displayed above. Note that only the write method is contained within the while loop as the object only needs to be created once at the start.
Using this approach you can connect multiple mbeds on different ports and control them from LabVIEW. The vi's have been designed to align as closely as possible with the api so looking in the Handbook should help explain what each method does. As its using the RPC the vi is directly calling the methods in the api.
Using RPC with Custom Code¶
The RPC-Interface-Library provides a mechanism for quickly adding RPC functionality to your own code. This LabVIEW library includes support for the RPCFunction and RPCVariable Objects. You can tie an RPCFunction or RPCVariable object to the corresponding object on mbed. You can then run the function or read and write to the variables which are attached.
The RPCVariable read and write blocks have both numeric and string inputs and outputs. You should wire to the appropriate one according to the type of variable it is corresponds with on mbed. The motor control IMU display demo at the bottom of the page show examples of these VIs in use.
Information
If you need to write your own entirely custom RPC command then you can use the RPC method that is part of the mbed class. Don't use the RPC methods in the Serial or HTTP class as this will prevent you from swapping transport mechanisms in the future. You can use this RPC method to create new interface classes. The name and method are passed as strings and the arguments are passed as an array of strings.
Here are the mbed vi's we've created to communicate between mbed and LabVIEW:
- mbed-ni.zip - mbed read and write VI's, plus Hello World examples
Download these and use them as components in your LabVIEW designs.
The Protocol¶
To keep things simple, we're assuming the communication between LabVIEW and mbed is a line-based text protocol. That means every 'packet' between LabVIEW and mbed is a string followed by a newline character (n). The mbed-read.vi returns a line read from mbed every time you run it, and the mbed-write.vi writes a string to the mbed every time you run it, so you can use this however you want.
Whilst the line string is the underlying data, there are also some common cases we've added support for such as sending single numbers, or comma separated value (csv) 'packets'. The inputs and outputs supported are:
Serial Communication With Labview Tutorial Blocked
- A string (e.g. 'hello' is transferred as 'hellon')
- A number (e.g. 1 is transfered as '1.0000n')
- An array of strings (e.g. ['foo', 'bar'] is transferred as 'foo,barn')
- An array of numbers (e.g. [1, 0.5] is transferred as '1.000,0.5000n')
These make it easy to work in LabVIEW without having to do lots of packing/unpacking/conversion yourself.
mbed Read Hello World¶
A simple labview example is included that plots the state of an AnalogIn input, which looks like:
And here is an example program to send some data:
The resulting output once the mbed COM port number has been selected in the VISA control, and when modifying AnalogIn, looks like:
mbed Write Hello World¶
A simple labview example is included that controls the brightness of LED1 and LED2, which looks like:
Labview Tutorial Pdf
And here is an example program that responds to the commands:
The control panel looks like:
Here is an example of closed loop PID control of a motors position using LabVIEW. LabVIEW is very useful for experimenting with control because it allows you change the control constants on the go and you can graph the outputs of both demanded and actual response to see how well the control system is performing. Its also possible to pass any signal into your system as the demanded value, in this case a slider is used but this can be replaced with a function generator.
The basic serial version is for the serial examples is here:
Also, RPCVariable objects can be used to pass the position of the wheel as a percentage of one rotation and the output to the motor. The Motor that has been used is from Pololu and includes an encoder. The wheel position is found using the QEI library and the motor is controlled using an L293D and the Motor library.
Here is the front panel and the block diagram for the LabVIEW vi. (Pictures of the setup coming soon!)
The red line shows the demanded value and the white line the actual motor position. As the motor has a gear box its quite slow and theres a lot of damping this means that the control is very simple and changing Kp just changes how long it takes to get to the demanded value. However at some values the porportional output to the motor becomes too low to actually drive the motor before it reaches the demanded position, in which case the integral control can be used elimiate the error.
Here is the code that was running on mbed for this demo.
As well as control LabVIEW can also be used to visualise data in a much more intuitive way than just printing it to a terminal. This is the LabVIEW VI featured on Aaron's IMU page where its used to show the output from the IMU. Its gives a visual output which shows the measured orientation. Its then a lot easier to see what the values mean and how errors acumulate than when you're looking at a long list of figures at a terminal.The program running on mbed uses the example program on the IMU page but with a few changes. As the IMU class doesn't support RPC, RPCVariable objects were used to pass the yaw pitch and roll variables and so a few lines were altered in the example program:
Labview Usb Serial Communication
This is the Block diagram for the VI which visualises the output.